The Making Process of Kobaien Inksticks
There is no window in the room that collects the soot that is the raw material for ink. 100 flames are burning in one room. In the work of collecting soot, one craftsman has two rooms to take care of. In other words, a craftsman handles 200 flames.
He is very careful about the amount of flame, and adds oil every hour. He prepares for the next wick in the meantime.
At the end of the Edo period, research on how to make ink was very advanced. The documents and materials of the time left by Kobaien’s successive leaders have been handed down to the present day.
At Kobaien, they continue to produce the highest quality oil smoke ink using a secret manufacturing method that has been passed down from generation to generation.

01
Collecting soot
A skilled craftsman pours pure vegetable oil into the jar and lights the wick made of rushes. He then covers the jar with an earthenware cover and collects the soot from the inside. He turns the jar every 20 minutes so that the soot does not stick unevenly.
This is a very delicate process that requires a lot of attention to the heat and the amount of oil.
02
Dissolving glue
He puts the fine glue into a copper jar about 30 centimeters deep.
He then slowly warms it over time with hot water at 70 degrees Celsius to make a solution of the glue.
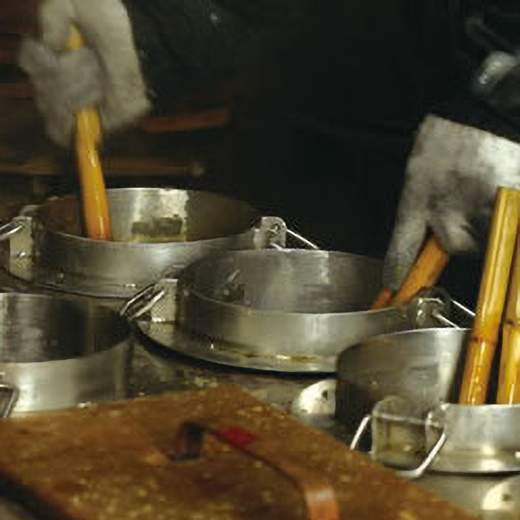
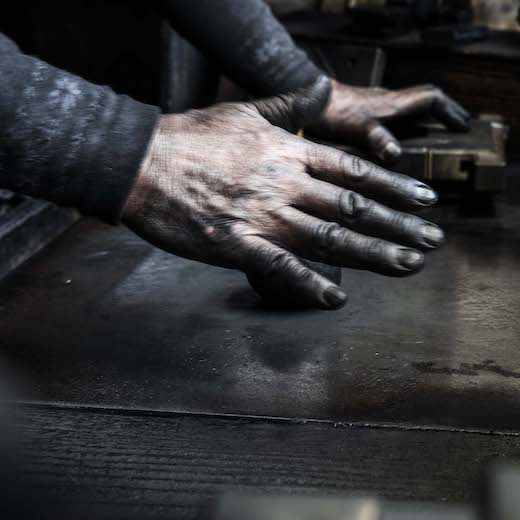
03
Mixing and kneading
Next, he mixes the carefully prepared soot and solution of glue in a ratio of 100 parts soot to 60 part glue.
At this time, he also adds fragrance and kneads them well. The quality of the ink depends on how well it is kneaded.
04
Forming
The craftsman puts the well-kneaded glossy ink into the wooden mold made of pear wood, on which the letters and designs are carved.
The inkstick size, called “Icchokata”, weighs roughly 15 grams, but when it is put into the wooden mold, it weighs about 25 grams because there is still a lot of water in the ink.
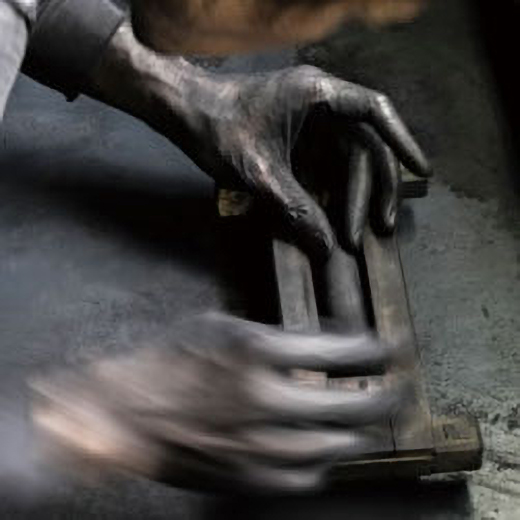
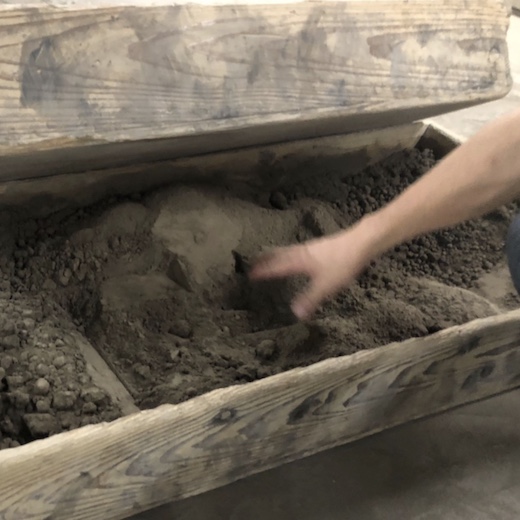
05
Drying with ash
Once the ink has hardened to a certain degree, the craftsman removes the ink from the wood mold and allows it to dry.
He first dries the ink by placing it in moist, watery wood ashes. Later, he changes the ash to a less moist one and continues to dry the ink.
This drying process takes about a week for small inks, and about a month for large ones.
06
Natural DRYING
Ash drying removes about 70 percent of the water from the inksticks. Then the craftsman hangs the inksticks from the ceiling with a straw cord to allow it to dry naturally.
This period lasts about one to six months.
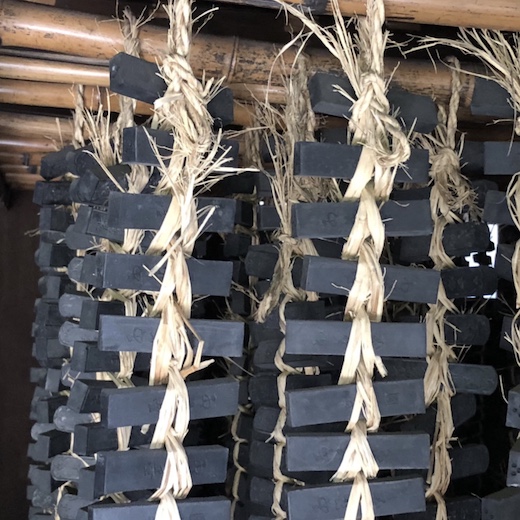
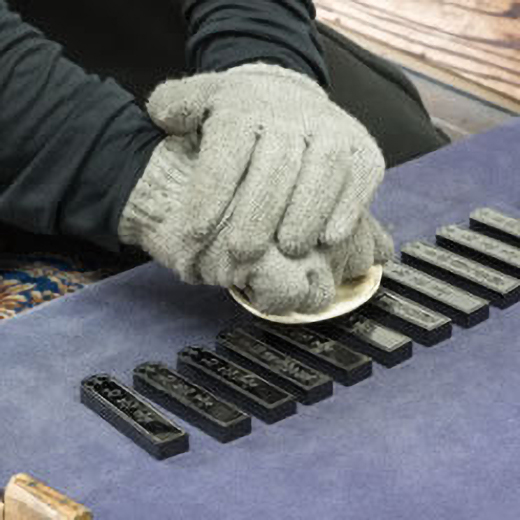
07
Polishing
After the natural drying process is complete, the craftsman carefully washes the ash-covered ink with water one by one.
He then roasts the inkstick over a charcoal fire to slightly soften its surface and polishes it with clam shells.
This process gives the inkstick a beautiful luster.
08
COLORING
The inkstick is left to dry naturally for a while again.
Finally, the craftsman uses gold and silver powders, and various other pigments to color the inkstick.
The unique patterns of Kobaien’s inkstick become more beautiful and vivid with this coloring.
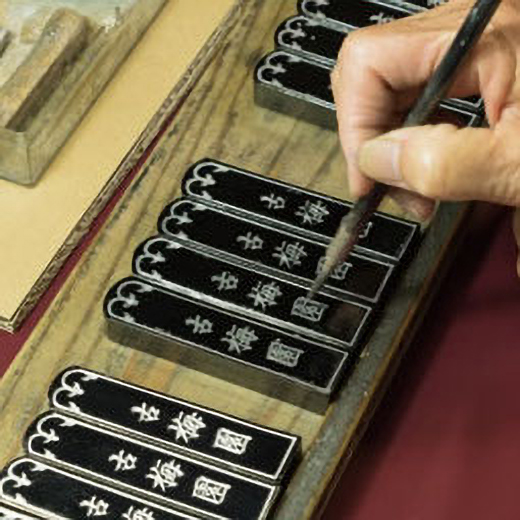